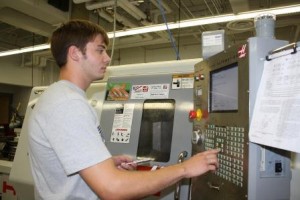
DUBOIS – A fresh renovation to the engineering lab at Penn State DuBois will be beneficial to both students, and some local businesses in the powder metal and manufacturing industries who can take advantage of new equipment and services.
“The goal was to increase the capabilities of our lab for teaching students, as well as increasing the flexibility we have to work with local companies on research projects,” said Assistant Professor of Engineering Craig Stringer.
Financed, in part, by a grant from the Commonwealth of Pennsylvania’s Ben Franklin Technology Development Authority, improvements to the lab include new electrical and ventilation systems for safety, convenience, and added equipment capacity. However, the real gains for industry and education come with new equipment and better utilization of current equipment, like a state-of-the-art Computer Numerical Control (CNC) mill and lathe. It’s a machine which can be programed to automatically produce precise dimensional metal parts at an impressive pace. Many parts made by machines like this are used in the fabrication of goods for industries such as the automotive industry, powder metal industry, and other key manufacturing areas relevant to the regional area.
Other improvements include equipment used to test the characteristics of material powders before they are pressed into a solid piece. Powder can be placed into a powder feeder and within seconds the machine can determine the size of the powder particles, the volume fraction of sizes, and print a detailed report recording all the data. Many local companies and campus engineering students have already taken advantage of the equipment to check their powder mixtures from season to season, or from different powder vendors, troubleshoot product quality issues within a production line, and formulate new materials mixtures for required projects. Students can now see how to choose the proper powder characteristics for the job they’re doing, and meet specified requirements of their applications.
“The properties of the material dictate the properties of the part,” Stringer said. “We look at the powder properties, the design process for a particular part, and the way it needs to be produced, and decide what powder characteristics will work best for the final product.”
Another recent addition to the lab is equipment used for measuring the dimensional change of materials brought on by temperature, or the materials’ thermal expansion.
“This will allow us to understand the dimensional change and the materials’ behavior under different atmospheric conditions, heating and cooling rates, and other processing variables,” Stringer mentioned.
Offering the opportunity to perform these analyses to local manufacturing companies, Stringer said, can be an enormous help to those in the industry looking to break ground with new products. In fact, Stringer, his colleagues, and his students are assisting companies on several projects at this time that are confidential.
“Some projects won’t even be out for three to five years,” Stringer said. “Companies like to keep these things under wraps until they’re ready to start production.”
For students, they’re putting their hands deep into the work that they want do in their career, rather than just learning the concepts through classroom lectures.
“You’re able to apply what you learn in the classroom to a project here in the lab, and it really helps you learn what you need to do,” said third year mechanical engineering student Justin Kerr, of Punxsutawney. Kerr said he plans to pursue a career in the manufacturing industry, and already feels prepared for his first job thanks to his work in the lab. “It gives you an edge. I’m learning things here that students at other schools might not have the opportunity to learn if they’re only in a classroom.”
The lab and its new equipment are even saving money for the campus engineering program by making the program more self-sufficient. Stringer noted that metal rods, called tensile bar specimens, are now produced in-house in the Penn State DuBois lab. Tensile bar specimens are placed under stress in a machine until they break; the amount of pressure a specimen can withstand before breaking tells engineers how strong the metal is. This lab exercise teaches students a processes used by manufacturers to test metals around the world. Making these tensile bar specimens in the labs, as opposed to buying them, adds up to big savings.
“This cost us $110 to buy,” Stringer said, holding up a single specimen, and noting that the lab can go through 20 of them each year. “We can now make it for $4.00. It’s a huge cost cutting measure doing this in-house.”
Steve Harmic, Penn State DuBois